・5Sが製造業をダメにする理由は?
・工場、製造業の実態は?
・収入を上げる方法は?
こんな悩みを解決できます!
高校卒業後、大手化学メーカー勤務歴14年経験。2022年に同業種に転職して年収200万円アップした私が解説します。
【今すぐ現状を変えたい方必見!】モグラ主任の公式LINEで完全無料プレゼント中!
「工場勤務×副業」で安定的に収入を得ましょう!
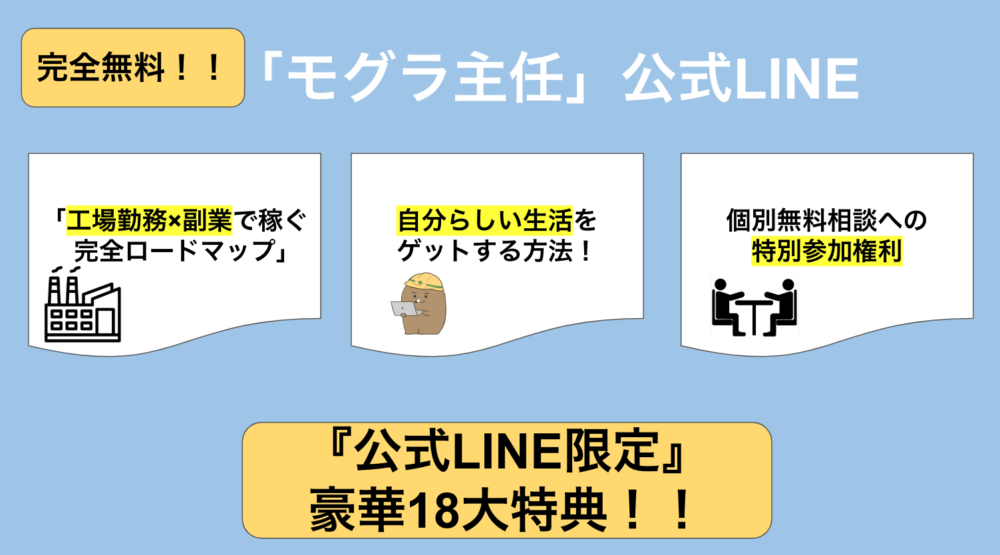
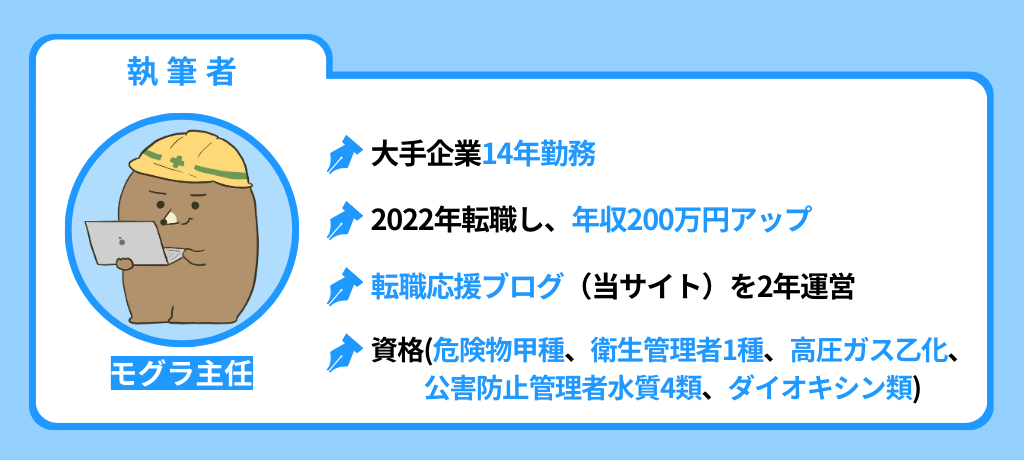
工場勤務の仕事内容
この記事での仕事内容は、化学、繊維工場における生産、製造管理についてです。
ライン作業やピッキングなどの仕事内容とは違いますでのその点ご理解ください。
工場の仕事内容も様々あります。
5S活動とは
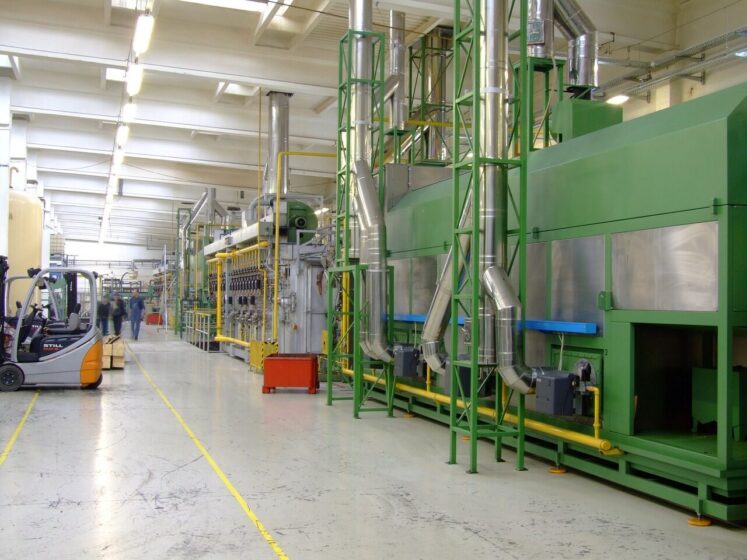
そもそも5S活動を正しく理解しましょう。解説します。
整理(Seiri):不要なものを処分したり、あるべき場所に片付ける
整頓(Seiton):必要な物を使いやすい位置で、すぐに取り出せるようにする
整頓(Seisou):整理・整頓がなされていることを前提に、清掃を徹底する
清潔(Seiketsu):整理・整頓・清掃により、常に清潔な状態を維持する
躾(Shitsuke):整理・整頓・清掃・清潔のルールを習慣づける
5S活動とは、上記の「整理(Seiri)」「整頓(Seiton)」「清掃(Seiso)」「清潔(Seiketsu)」「躾(しつけ)(Shitsuke)」の頭文字を取った言葉になります。
安全な生産を達成するために導入されており、生産現場やオフィスなどでも導入されている方法になります。知らない人はいないと言われるほど定着しています。
また、「3S」と呼ばれる場面も多いです。労働災害を防ぐ目的で欠かせない要素なっています。最近では病院や一般企業にも5S活動の導入が広がりつつあります。
職場のチェックリストとしても活用されてます!
5S活動が製造業をダメにした理由6選
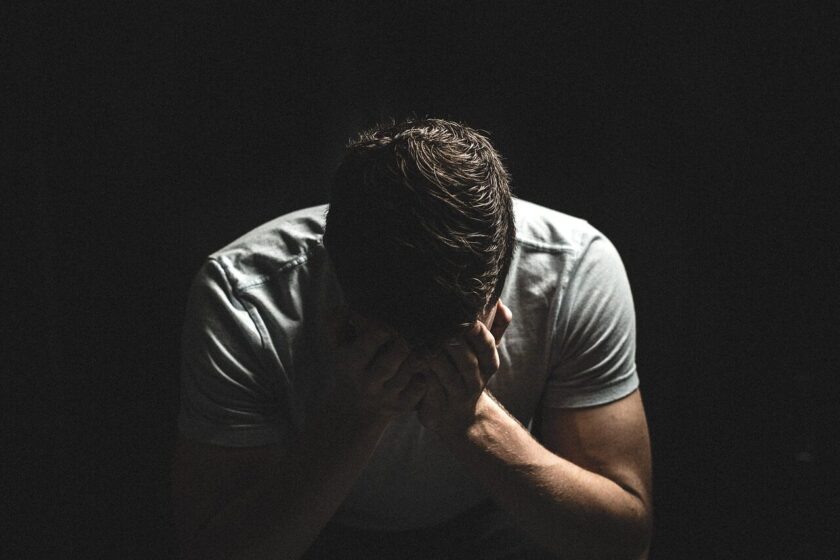
よく言われるのが「5S活動が製造業をダメにした理由6選」について解説します。ダメにする理由をよく理解して、うまく取り組みましょう。
- 5Sばかりが優先される
- 作業効率を低下させる可能性
- アイデアがない
- 水平展開が強要される
- 従業員の意識の差
- 従業員のモチベーション低下
5Sばかりが優先される
ダメにする理由は、5Sばかりが優先される点です。
本来の目的からかけ離れてしまうため。
実際に、安定生産が求められる職場で5Sばかりに時間を割いても、生産にあまり効果はありません。結果的に、生産性の低下の懸念もあります。
そのため、5Sばかりを優先するのは本来の目的とは異なります。
ただし、5S活動は安全面において重要なポイントです!
作業効率を低下させる可能性
続いて、ダメにする理由ですが、作業効率性を低下させる可能性があります。
綺麗なレイアウトや方法が逆に使いづらいから。
私の実体験ですが、見た目を綺麗にするレイアウトを採用し、作業エリアから離れた位置に設置したゆえに、作業効率が悪くなった経験があります。
ですので、見た目などを優先するあまり作業効率を低下させる可能性が懸念されています。
アイデアがない
5S活動で多い内容ですが、アイデアがなくなる点が挙げられます。
継続して活動すると、改善案が思い浮かばなくなります。
例えば、事務所内の5Sも数十個は改善可能ですが、それ以上を考えるとなかなか思い浮かばなくなります。
その結果、アイデアがなく活動が中断してやらなくなる事象が多いです。
事例は調べるとたくさんあるので参考にしてください!
水平展開が強要される
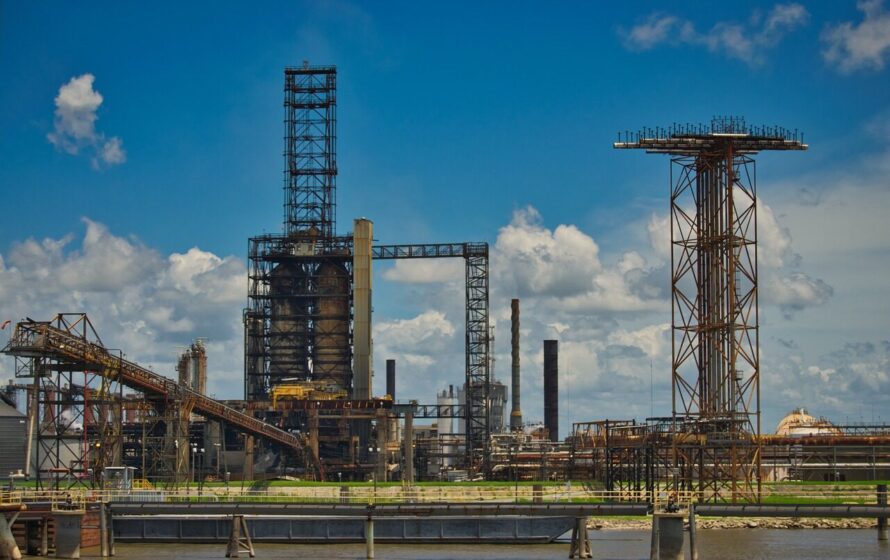
ダメにする理由として、水平展開が強要されることが挙げられます。
理由は、いい活動を展開するが、必ずしも効果的かは不明なため。
例えば、デジタルツールを導入して5Sを確率しても年齢層が高い部署ではうまく活用できません。
ですので、水平展開を強要される結果逆に作業しづらくなったりします。
従業員の意識の差
次にダメにする理由は、従業員の意識の差がある点です。
なぜならば、やりたがらない従業員がいるから。
実際に、私の職場にも5S活動を頑なにやらない人がいました。やる意味とがないと言っており、参加すらしませんでした。
そのため、従業員の意識の差が生まれ組織をダメにする可能性が含まれています。
積極的に活動をしてアピールしましょう!
従業員のモチベーション低下
従業員のモチベーション低下の可能性があります。
理由は、5S活動の指示が多いため。
私の実体験ですが、安全のために5S活動してください。と依頼が日常的にありました。何度やっても終わりがないので従業員のモチベーションが低下します。
なので、従業員のモチベーションが低下してダメにすると言われています。
5S活動はやって当たり前の雰囲気もあります。腐らずやりましょう!
5S活動の目的3選、歴史
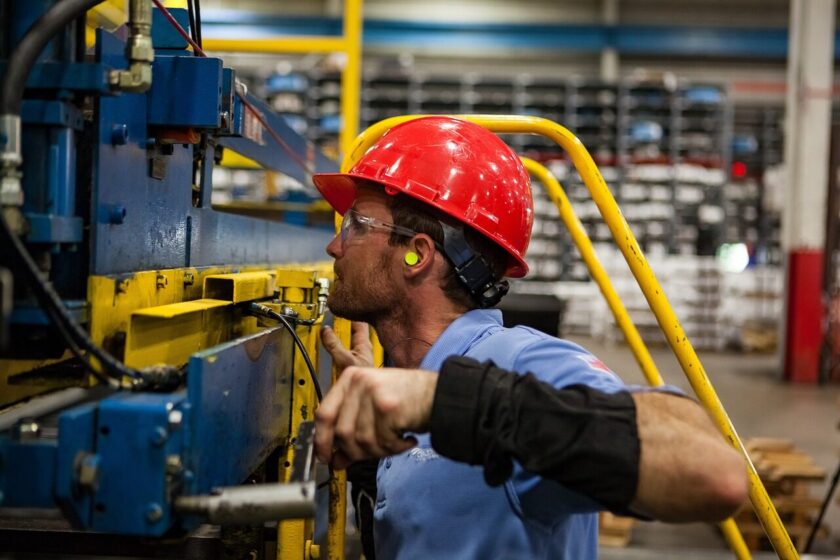
5S活動の目的は大きく3選あります。それぞれ詳しく解説します。
- 安全面の確保
- 業務効率の向上
- 労働環境の整備
安全面の確保
5S活動の目的1つ目は、安全面の確保になります。
なぜなら、5Sが行き届いていないと不安全な状態が多い職場となります。
例えば、作業で使用した工具を歩行エリアの床に置いたまま放置すれば、別の方が歩いた際に躓いたり、転倒する危険があります。
そのため、整理整頓され清掃が行き届いた職場は安全面が向上します。
ストレスなく働ける労働環境も重要です!
業務効率の向上
5S活動の目的2つ目は、業務効率の向上が挙げられます。
理由は、スムーズに作業するためには重要です。
私の実体験ですが、素早くトラブル処置したいにも関わらず、工具を取りにくいために10分ほど費やした経験があります。たかが10分ですが、されど10分です。
ですので、こういった作業効率を下げることなく、作業するためには必要になります。
労働環境の整備
5S活動の目的3つ目は、労働環境の整備になります。
なぜなら、従業員同士がストレスなく仕事するため。
例えば、整頓ルールがなく、不用品が多いと探す手間がありストレスになります。誰でもわかりやすいように配置しておく必要があります。
そのため、従業員のモチベーションを下げないためにも労働環境の整備を心掛けてください。
全員が気持ちよく仕事できるようにしましょう!
5Sの歴史
5S活動の歴史については解説します。
1955年頃にTOYOTAの「トヨタ式5S」活動がきっかけとして広く採用されています。
大きな特徴として、安定の生産活動を行いながら、生産性の向上にも貢献する仕組みとなっています。
特に最初の活動は、物の置き場所を統一からスタートしました。
「必要な物がどこにあるか探す時間」は意外にも業務の手を止めると言われています。
資料整理も第一歩になります!
5S活動のメリット10選
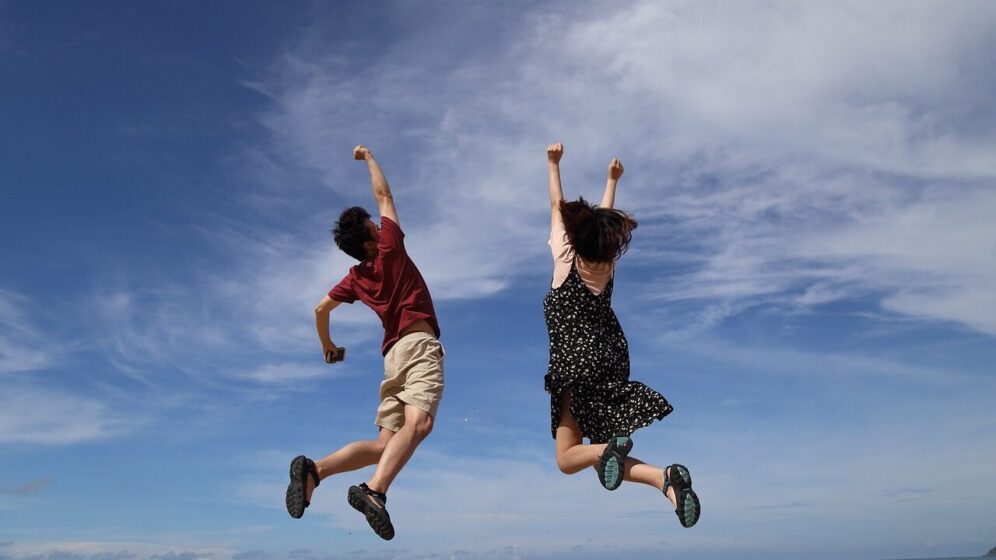
続いて、5S活動のメリット10選について徹底的に解説します。組織として取り組むことでより大きな成果を出すことができます。
- 安全面の向上
- 綺麗な職場で働ける
- 業務効率の向上
- コスト削減
- 製品の品質向上
- 従業員の士気が上がる
- 組織のコミュニケーションが良化
- 評価されやすくなる
- 社員の意識が変化
- 見学者にいい印象を与える
安全面の向上
まず、メリットとして安全面の向上が見込めます。
なぜなら、現場が安全な状態になるため。
私の実体験ですが、歩行ルートにダンボールなどの資材があると足をぶつけ転倒するリスクがあります。しかし、5S活動をすればそういった不安全な状態を排除できます。
結果的に、安全面の向上が見込めます。
製造現場において安全は最優先事項です!
綺麗な職場で働ける
続いてのメリットですが、綺麗な職場で働けます。
清掃の習慣化されれば汚れた状態が減るから。
例えば、5Sが習慣化されたら作業で汚した場合は速やかに清掃します。作業毎に清掃が習慣化されたら綺麗な状態が継続できます。
なので、5S活動を継続すれば綺麗な職場で働くことも可能になります。
業務効率の向上
5S活動がもたらす3つ目のメリットですが、業務効率の向上があります。
作業スペースの確保できるため。
実際に、作業スペースが狭い場所での作業は大変です。5S活動を行うことで、必要な工具を素早く見つけたりできます。
結果的に、効率よく作業が可能となり、業務効率が向上します。
工具入れがグチャグチャなことはよくあります!
コスト削減
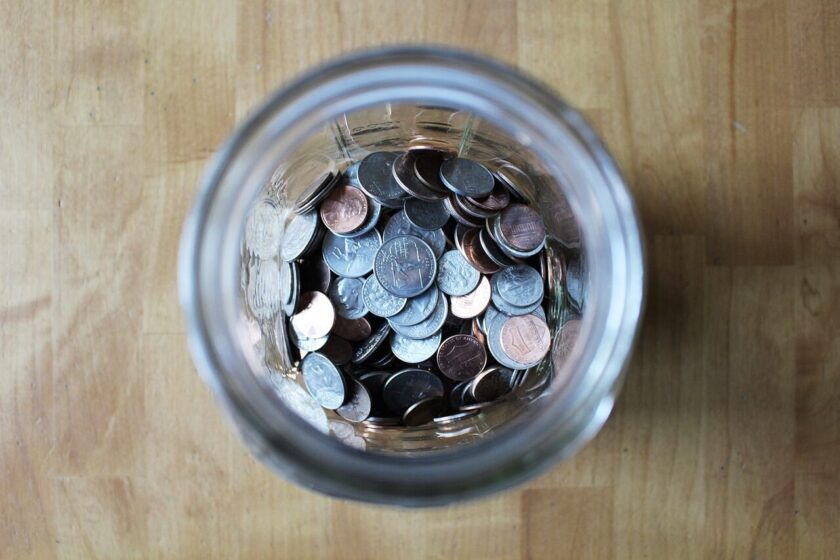
続いてのメリットは、コスト削減に繋がります。
必要な工具が紛失しなくなるから。
工場で働いていると必要な工具がよく紛失します。その都度必要な工具を買い替えると、コストが増加しますので、結果的にコストがかかります。
なので、5S活動で必要な工具の管理ができればコスト削減も期待できます。
備品が勝手に移動されるのはよくある話です!
職場でルールを決めておきましょう。
製品の品質向上
5S活動がもたらす5つ目のメリットですが、製品の品質が向上に期待できます。
なぜなら、異物混入や製品に傷をつけたりが低減できるため。
実際に生産現場は人的エラーやミスで異物混入や製品に傷をつけてしまう事案はよく発生します。運搬ルートの5Sが徹底されていればそのようなトラブルも事前に防げます。
繰り返しになりますが、5S活動で製品品質の向上に繋がります。
従業員の士気が上がる
5S活動が継続できていれば、従業員の士気が上がります。
ストレスなく作業に集中できるから。
私の経験談ですが、必要な備品や工具がいつもの位置にないと探す手間が発生しストレスになります。トラブル対応時に工具を探すのは非常にストレスです。
なので、5Sが継続できれば従業員は集中して作業に挑めます。
後で戻そうとしていても忘れてしまい変な場所にあったりします!
組織のコミュニケーションが良化
先ほどと似たメリットになりますが、組織のコミュニケーションが良化します。
理由は、作業がスムーズに進むため。
実体験ですが、先輩と作業していると必要な備品を取りに行かされる場面があります。その際、すぐ持って来れないと仕事が遅い、理解していない。などと言われてしまいます。
そのため、5Sで整理整頓されていれば、スムーズな作業ができ結果的にコミュニケーションが改善します。
評価されやすくなる
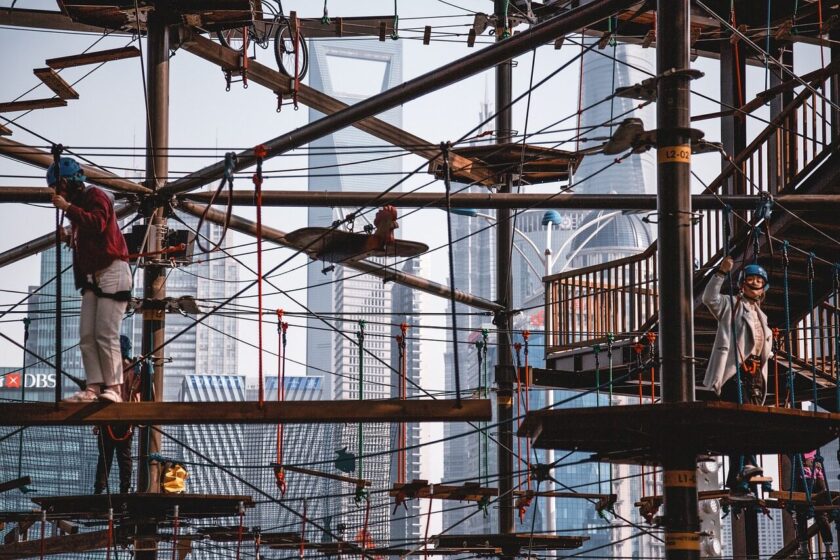
続いてのメリットですが、評価に繋がる場面があります。
あなたのアピールになるため。
例えば、5S活動を積極的に行う人は少なく、率先して行動する方は評価されやすくなります。上司から依頼があった時は素早く対応するのもおすすめです。
100%評価されるわけではありませんが、しっかりと行動することであなたの評価にも変化する可能性があります。
社員の意識が変化
5S活動を継続すれば、社員の意識の変化にも期待できます。
理由は、5Sに習慣が身に付くことで行動が変わるから。
実際に、綺麗な状態を汚すのは気持ちのいいものではありません。他の従業員が綺麗な状態にしていれば、従業員の意識も変化します。
そのため、5S活動を展開すれば、社員の意識改革も可能です。
継続すれば少なからず綺麗な状態が継続できます!
見学者にいい印象を与える
5S活動の進め方
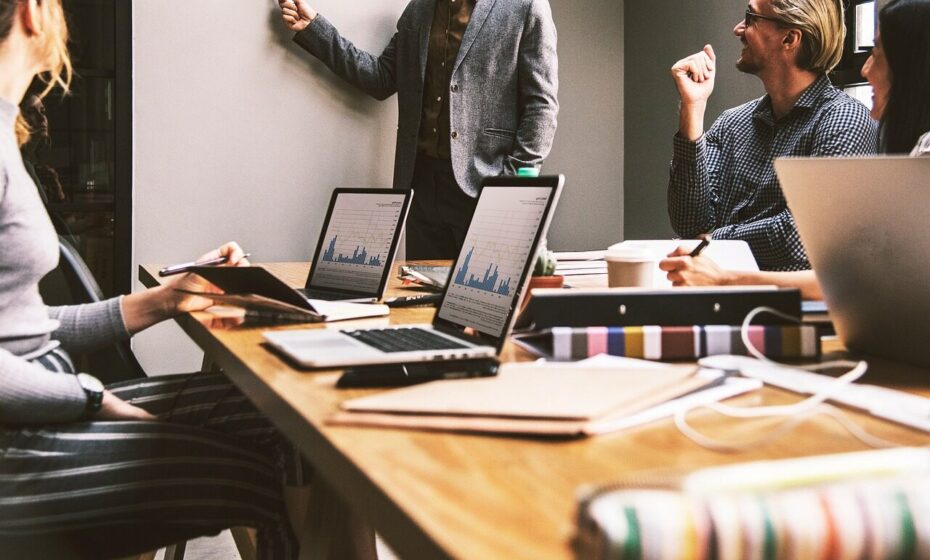
厚生労働省が発表した「5S活動事例」の内容から進め方について解説します。
介護関係の資料になりますが、他業種でも展開できます。
- 職場環境の整備
- 業務の明確化と役割分担(1)業務全体の流れを再構築
- 業務の明確化と役割分(2)テクノロジーの活用
- 手順書の作成
- 記録・報告様式の工夫
- 情報共有の工夫
- OJTの仕組みづくり
- 理念・行動指針の徹底
職場環境の整備
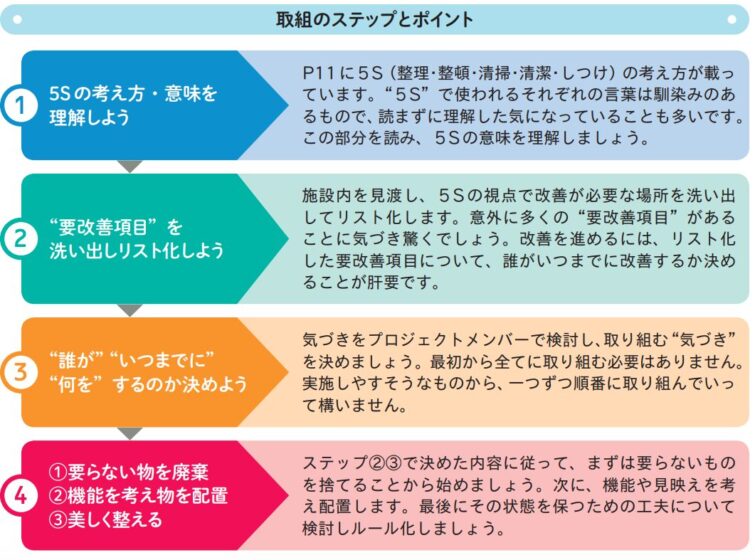
まず、大前提である5Sの視点での安全な介護環境と働きやすい職場をつくる。
必要なものがすぐに取り出すことができ、常に作業に取りかかることのできる状態を維持する。
例えば、置き場所が決まっておらず、床に置かれたもので転んで怪我をしてしまうなど、予測しない事故が発生することも多くなります。
5Sのために職場環境の整備をしましょう。
業務の明確化と役割分担(1)業務全体の流れを再構築
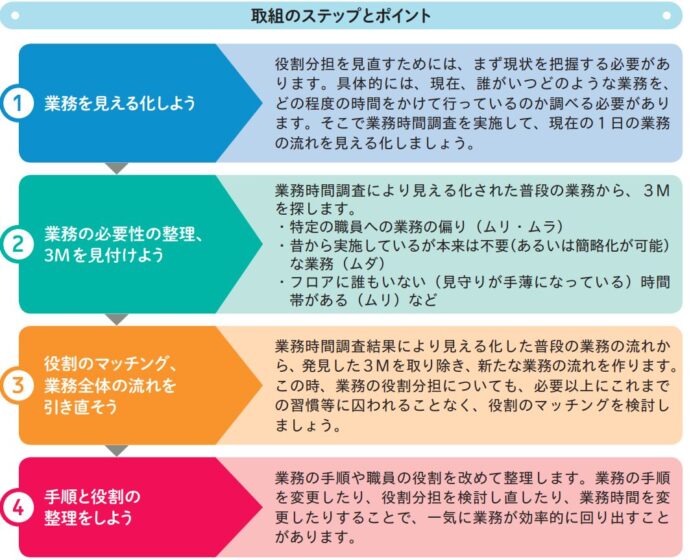
業務の明確化と役割分担の見直しにより、ムリ・ムダ・ムラ(3M)を削減して業務全体の流れを再構築する。
やみくもに、5Sを始めるのではなく業務の全体の流れを再構築すると効率的にできます。特に3Mの観点から進めるのがおすすめです。
手順と役割の整理をしましょう。
ムリ・ムダ・ムラ(3M)は組織全体で検討してください!
業務の明確化と役割分(2)テクノロジーの活用
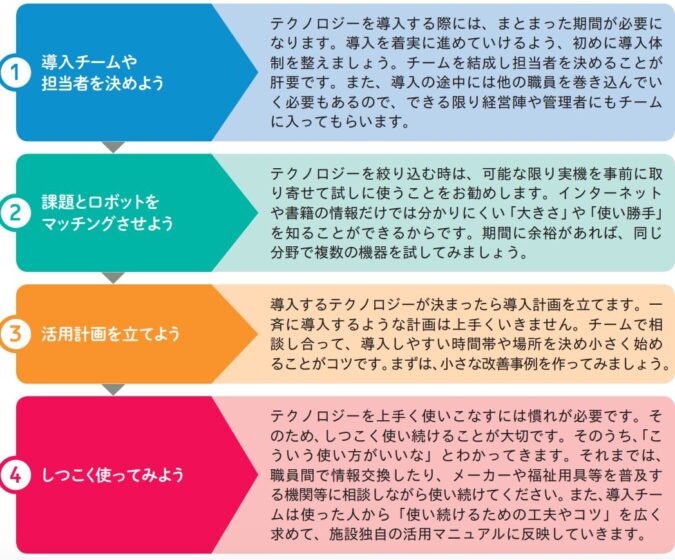
テクノロジーなどの活用により、職員の業務を見直し、身体的・心理的負担を軽減する。
介護ロボットなどのテクノロジーを用いることで、介護現場にゆとりの時間を生みます。人手不足にも一定の効果があると期待されています。
また、注意点としてはテクノロジーの導入前にはできる限り実機での検証を実施しましょう。使用方法などに慣れておく必要あります。
テクノロジーの導入は小さく始めましょう。
手順書の作成
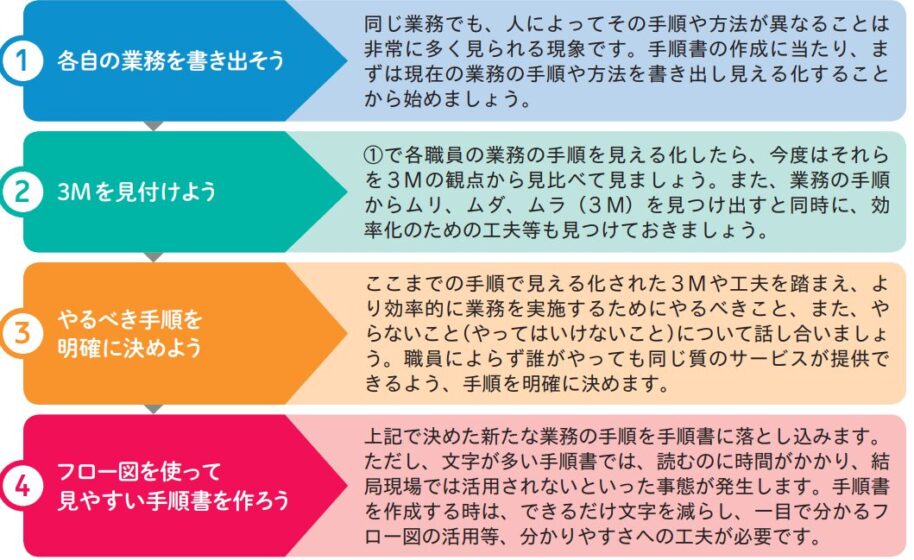
職員の経験値、知識を可視化し、サービスレベルを底上げする。
職員全体の熟練度を向上し、個別ケアに柔軟に対応する。
手順書は単なる業務マニュアルではありません。また、手順書作りでのポイントは、職員の経験値を見える化することも可能です。
以上の点を考慮しながら手順書の作成をしましょう。
記録・報告様式の工夫
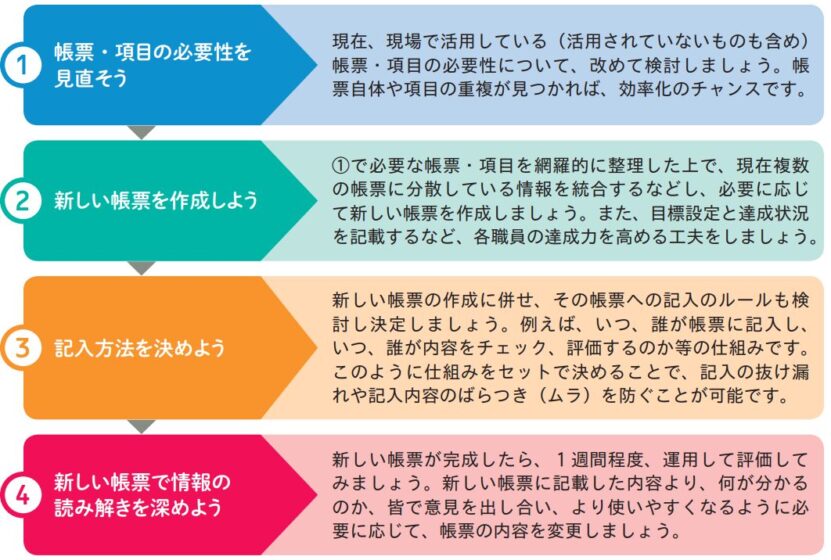
項目の見直しやレイアウトの工夫等により、情報の読み解きを容易にする。
不要な文書や整理できる項目を見つけるだけでなく、「なぜ文書を作成しているのか」といった本来の目的に気づくことができる。
特に実施する際は、目標設定と達成状況を記載するなど、各職員の達成力を高める工夫をしましょう。
もし、現在既に何らかの様式がある場合には、それが使いやすい形に変更など検討してください。
情報共有の工夫
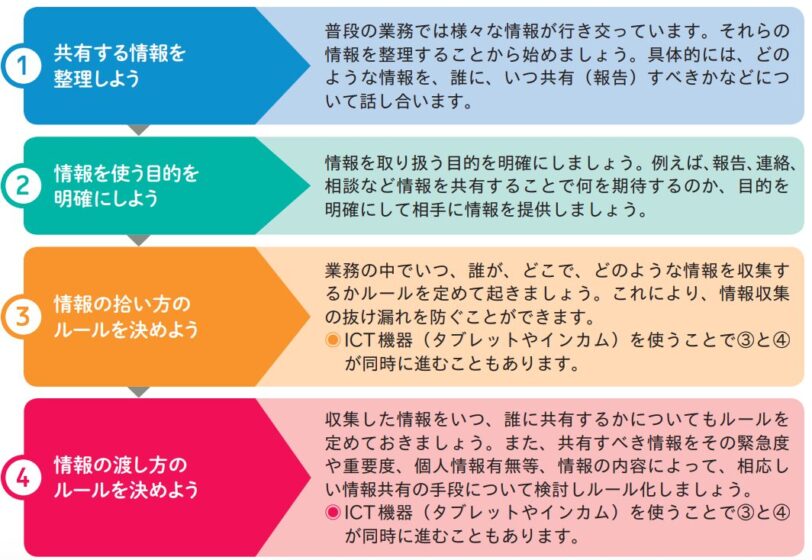
ICT機器を用いて転記作業の削減、一斉同時配信による報告申し送りの効率化、情報共有のタイムラグを解消する。
情報共有の手段としてICT機器は非常に有効です。特に手による各帳票への転記作業は、ICT機器を活用することで楽になります。
口頭など行うと忘れやニュアンスが伝わっていない可能性があるので注意してください。
情報共有の工夫をしておくことでスムーズな業務ができます。
OJTの仕組みづくり
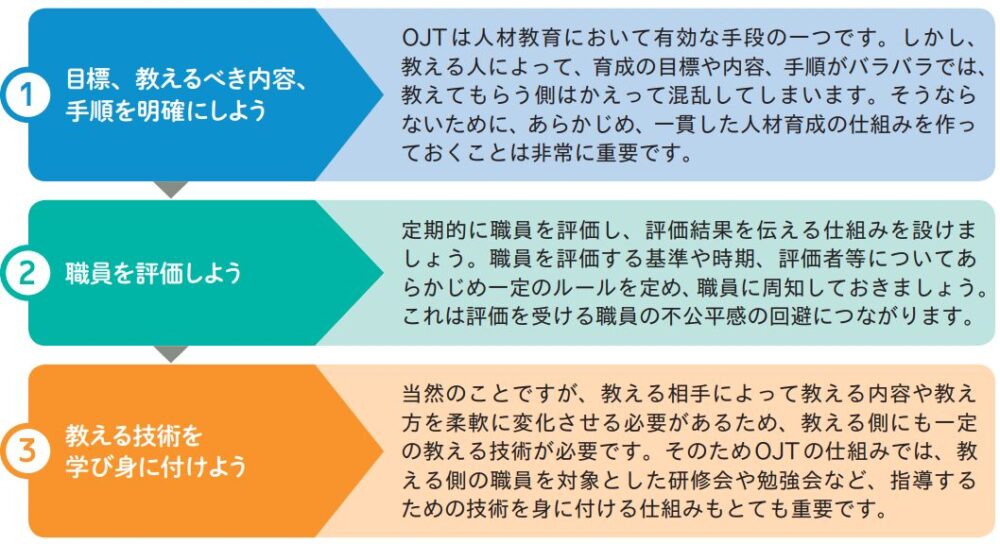
専門性を高め、リーダーを育成するため、教育内容の統一と教え方のトレーニングを実施する、教える仕組みをつくる。
OJT(On the Job Training)は非常に重要です。これは新人教育の場面だけではなくベテラン職員、マネジメント層等の人材育成においても幅広く活用できます。
OJTの仕組みづくりも意識しておくと継続もしやすくなります。
理念・行動指針の徹底
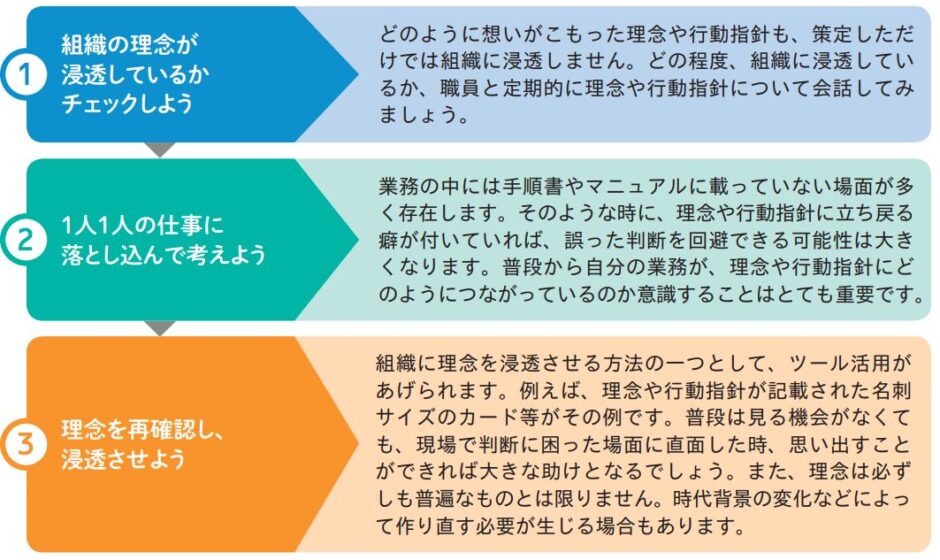
組織の理念や行動指針に基づいて、自律的な行動がとれる職員を育成する。
業務の手順書やマニュアルを作成しても、そこに記載されていないイレギュラーな事態が起こることもあります。
優先順位は、法人の理念・行動指針に立ち戻って考えることが重要です。
従業員に理念・行動指針の徹底しましょう。
5S活動でありがちなミス9選
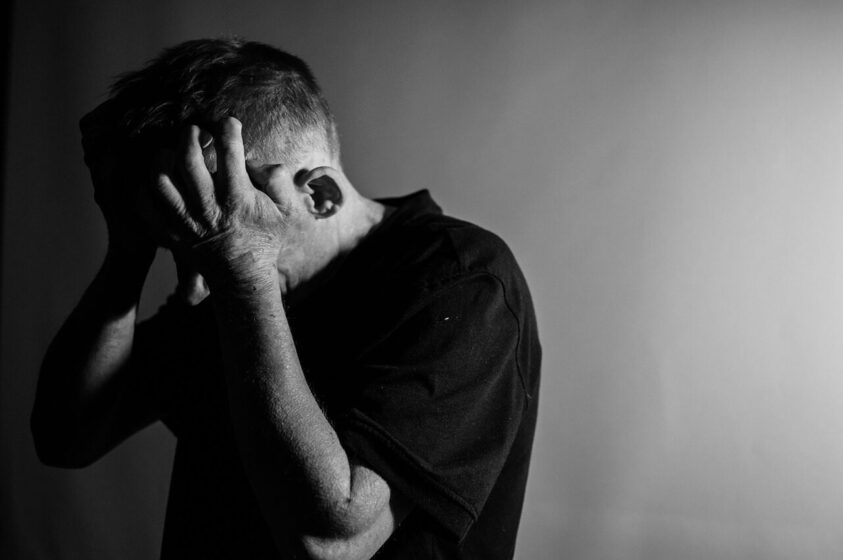
5S活動でありがちなミス9選について解説します。当てはまる方は要注意です!
- 5Sすれば効率性が上がると思い込んでいる
- やらされている感が強い
- ルールが複雑すぎると使いづらい
- 職場の統一感がない
- 習慣化しない
- 役職者が現場を知らない
- 5Sして当たり前だと思っている
- 5Sしても事故がゼロにはならない
- 事例をそのまま採用する
5Sすれば効率性が上がると思い込んでいる
5S活動でありがちなミスとして、5Sすれば効率性が上がると思い込んでいる点が挙げられます。
見た目にこだわり過ぎている可能性があるから。
例えば、整理・整頓のレイアウトを意識するあまり作業導線が悪くなった事例も多く存在します。結果的に、効率が悪くなってます。
そのため、総合的に考えず見栄えやレイアウトにこだわり過ぎるとかえって、効率が低下する懸念もあります。
現場作業員の声は絶対反映させましょう!
やらされている感が強い
続いて多い内容ですが、やらされている感が強い点があります。
依頼件数が多いと言われた内容しか改善しなくなります。
私の実体験ですが、トップダウンであれこれ指示があると、まずそれらを完了させる必要があります。1、2件ならいいですが、件数が多いと作業員は大変な苦労があります。
現場の作業員に対して、目的などを明確に伝えてないとやらさている感じが強くなり失敗しやすくなります。
ルールが複雑すぎると使いづらい
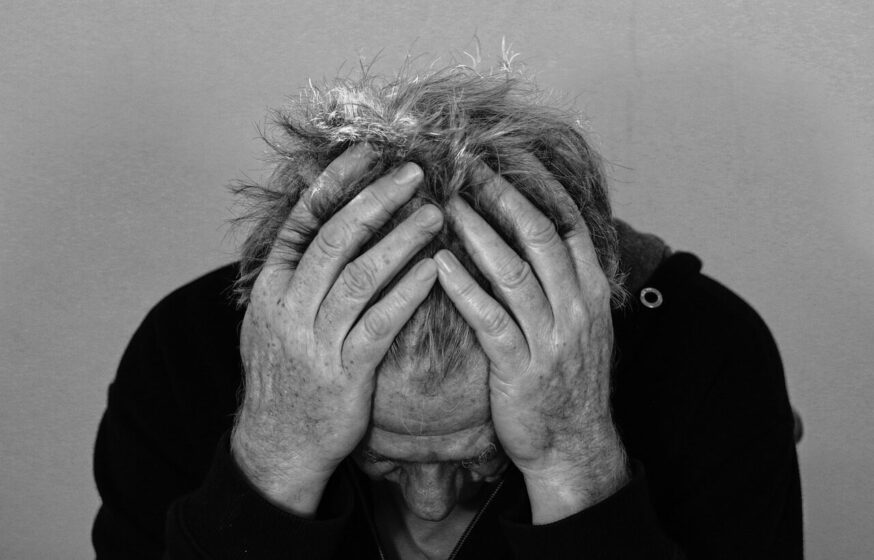
5S活動でありがちなミスですが、ルールが複雑すぎる点があります。
作業員は時間に追われている場面が多くより使いづらくなる。
例えば、トラブルが発生する場所は毎回同じではありません。離れた位置に工具掛けなどを設置すると毎回取りにくい手間が発生します。
また、使用する際、名前や使用場所を書くルールを厳しくしすぎると自分勝手に工具を持つようになったりします。
ルールは最小限で使いやすい環境を目指しましょう!
職場の統一感がない
こちらもよく挙げられる内容ですが、職場の統一感がない点が挙げられます。
理由は、個人個人が好き勝手に作成するため定着しなくなるから。
私の実体験ですが、40名の部署でしたが、使いやすさや表示方法は人それぞれです。自分好みに毎回カスタマイズされると統一感がなくなり、管理されなくなります。
ですので、職場では統一感を出すためにある程度意見集約や方向性を協議してから実施しましょう。
習慣化しない
5S活動でありがちなミスですが、習慣化しない。またはできない点です。
数える程度しか実施せず、終わらせてしまうため。
実際に、業業員への習慣化は時間がかかります。1、2回では身につきません。それを理解sてフォローなどしないと習慣化できず放置されるようになします。
習慣化できるまでは管理者が現場を巡回したり、声掛けを行ったりフォローしましょう。
5Sは習慣化がとっても大事!
役職者が現場を知らない
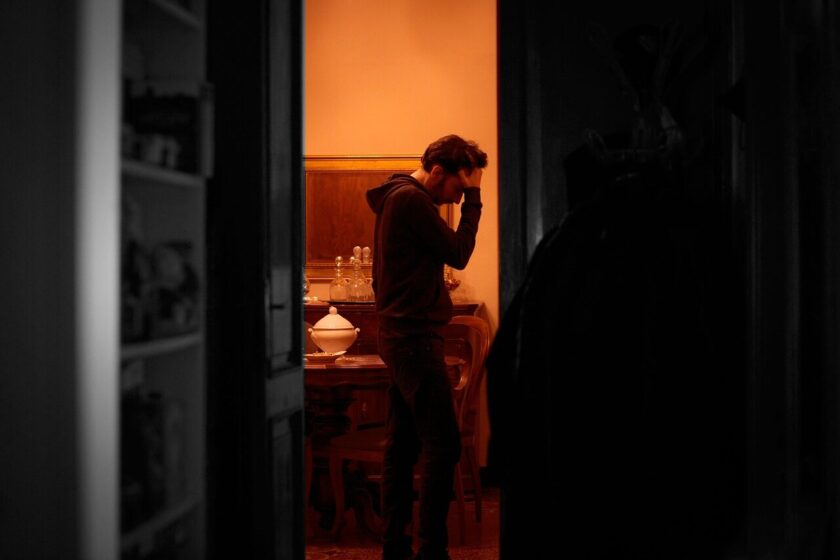
こちらも多い事案ですが、役職者の人が現場を知らない点があります。
工場見学の際に現場を知らないまま指摘するため。
例えば、本社勤務の方が現場の実態を知らず、見栄えだけを求めて指示を出しても、その状態が使いやすいとは限りません。
現場をあまり知らない方がたくさん指示すると、かえって作業効率が落ちる可能性があります。
5Sして当たり前だと思っている
続いて多いミスですが、5S活動が当たり前だと思っている。
感謝の意を伝えないと、やらされている感じが強くなります。
実際に、改善するのは現場作業員であり、忙しい業務の合間を縫って5S活動を実施してくれています。定期的に感謝を伝えましょう。
やって当たり前だと思う上司、先輩がいると続かなく可能性が高くなります。
どんな形であれ、感謝や認めてもらえるのは嬉しいです!
5Sしても事故がゼロにはならない
5Sを積極的に行えば、事故がゼロになると思い込むのは危険です。
5Sで全て防ぐのは困難になります。
例えば、5Sを徹底しても事故や災害が発生します。人が不安全な行動をした時や、機器が不安定な状態で発生してしまうことが多いです。
そのため、5Sだけすれば事故がゼロにはならないのでご注意ください。
事例をそのまま採用する
こちらも多いミスですが、事例をそのまま採用してしまう点があります。
他社の事例を採用しても、自社に合うかは分かりません。
実際に、デジタルツールなどを導入しても使いこなせなければ意味がありません。自社の人材が使いこなせるような事例からスタートしましょう。
ですので、事例をそのまま採用するのは少しリスクが高いので注意してください。
まとめ
今回は「5Sが製造業をダメにする」について、詳しく解説しました。最後に本記事の内容を振り返ってみましょう。
今回の記事の要点は以下のとおりです。
・5S活動も重要な役割がある!
・5S活動の進め方を理解しておく!
・収入を増やすなら副業がおすすめ!
今すぐ現状を変えたい方必見!
モグラ主任の公式LINEで完全無料プレゼント中!
本業だけの収入で大丈夫?工場勤務、三交代やめる方法はない?
あなたの『自分らしい生き方』の一歩目に役立つ内容なので、見逃さないようにみどりのボタンをタップして受け取ってくださいね!